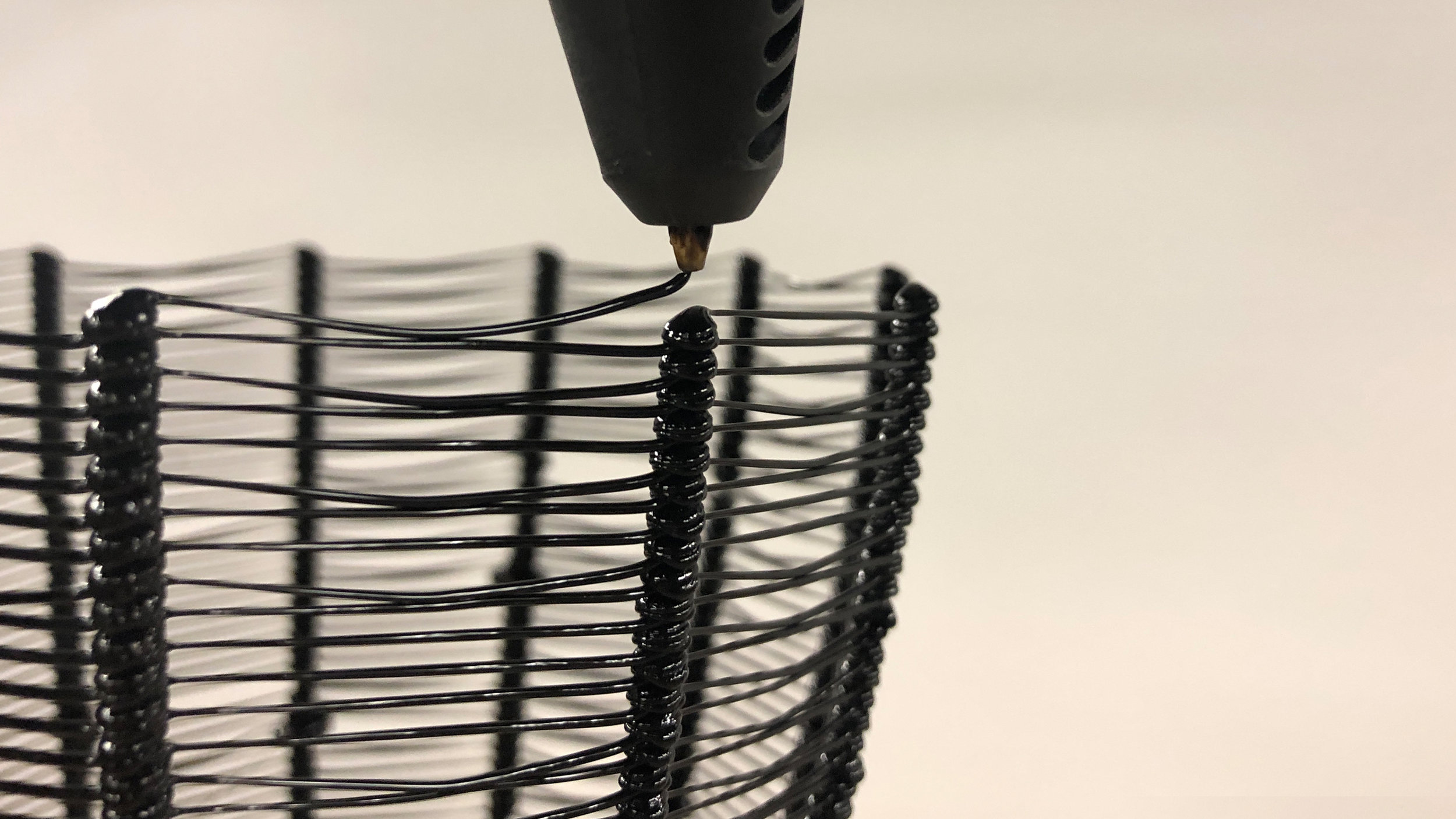
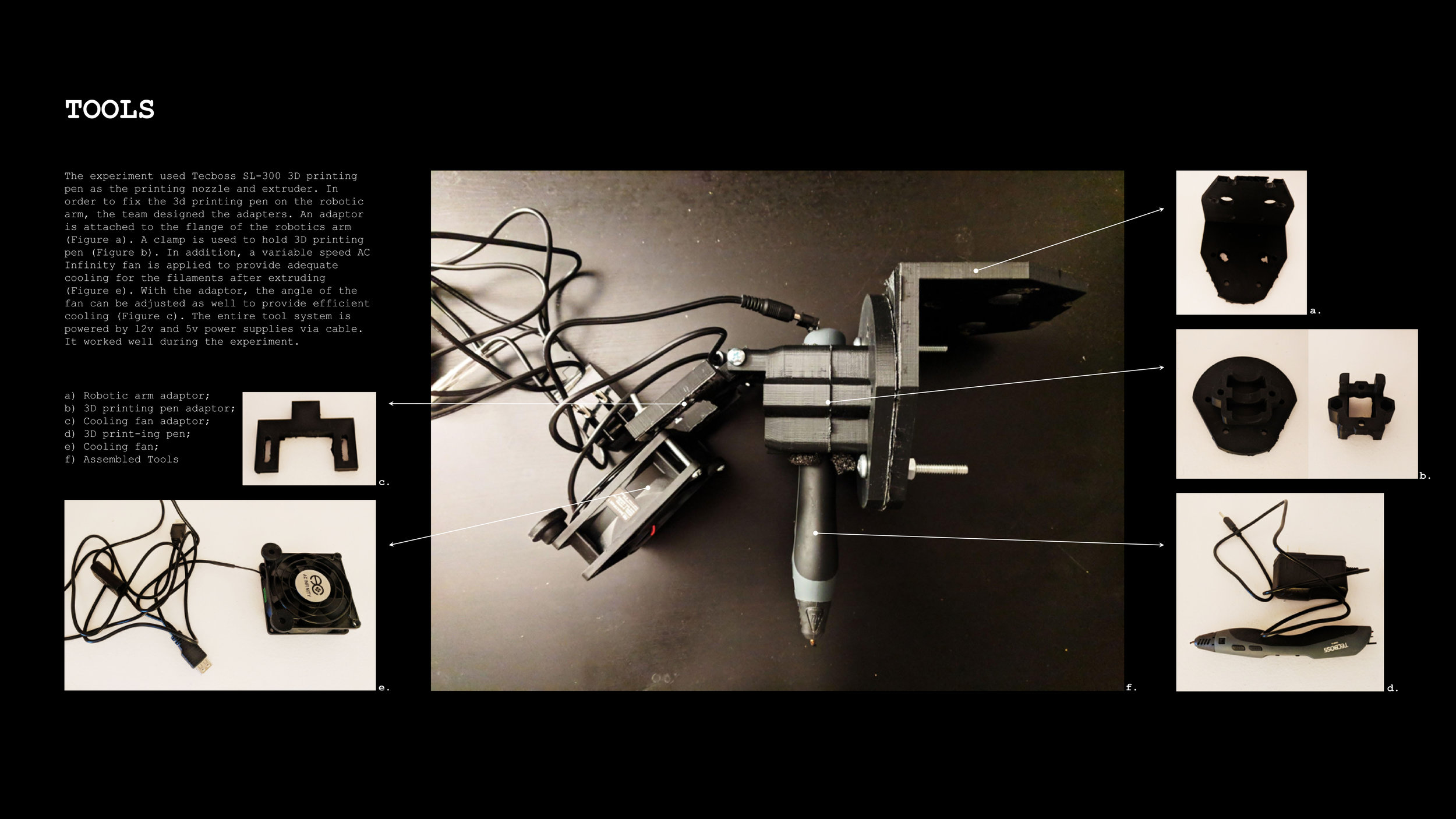
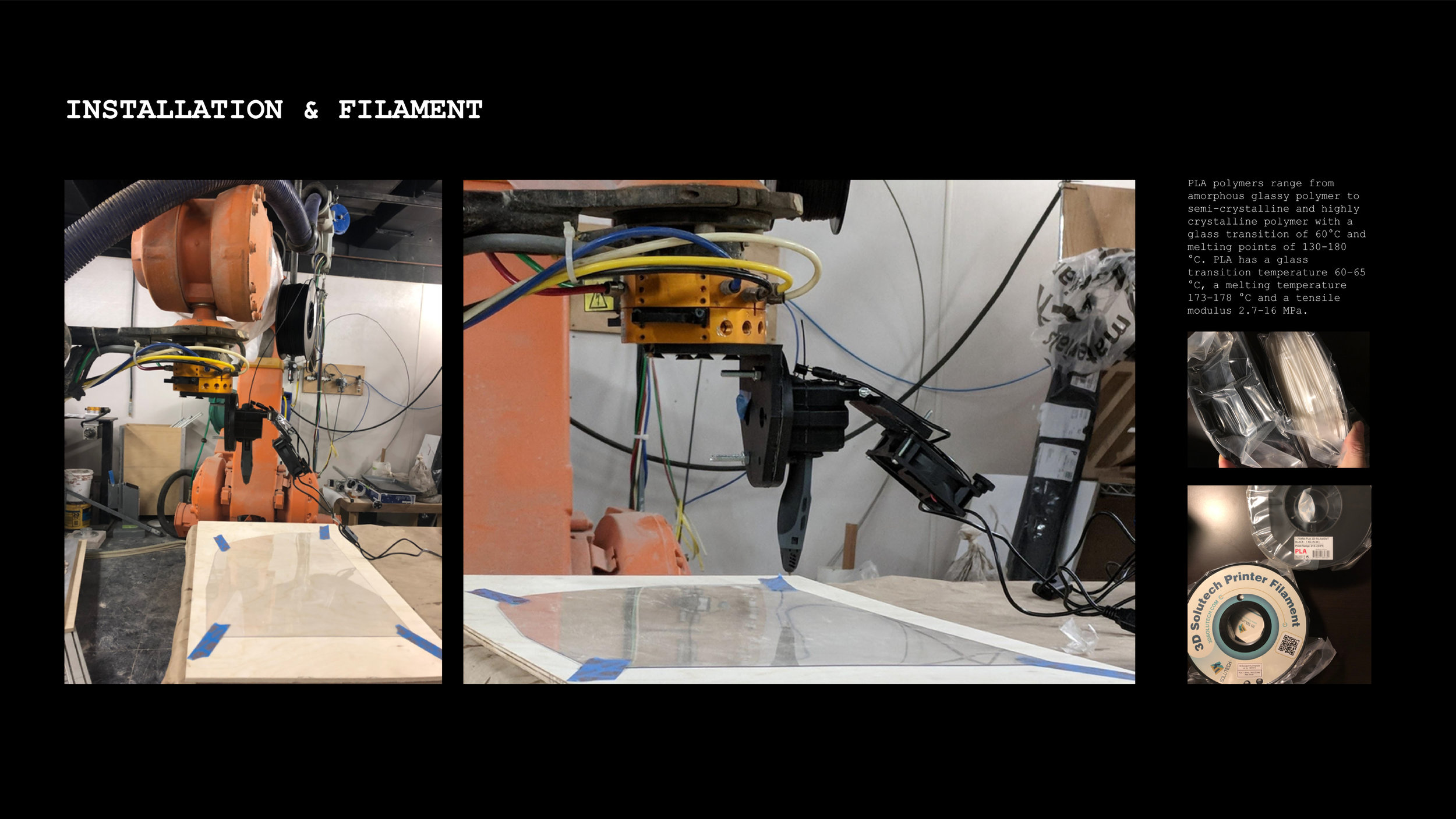
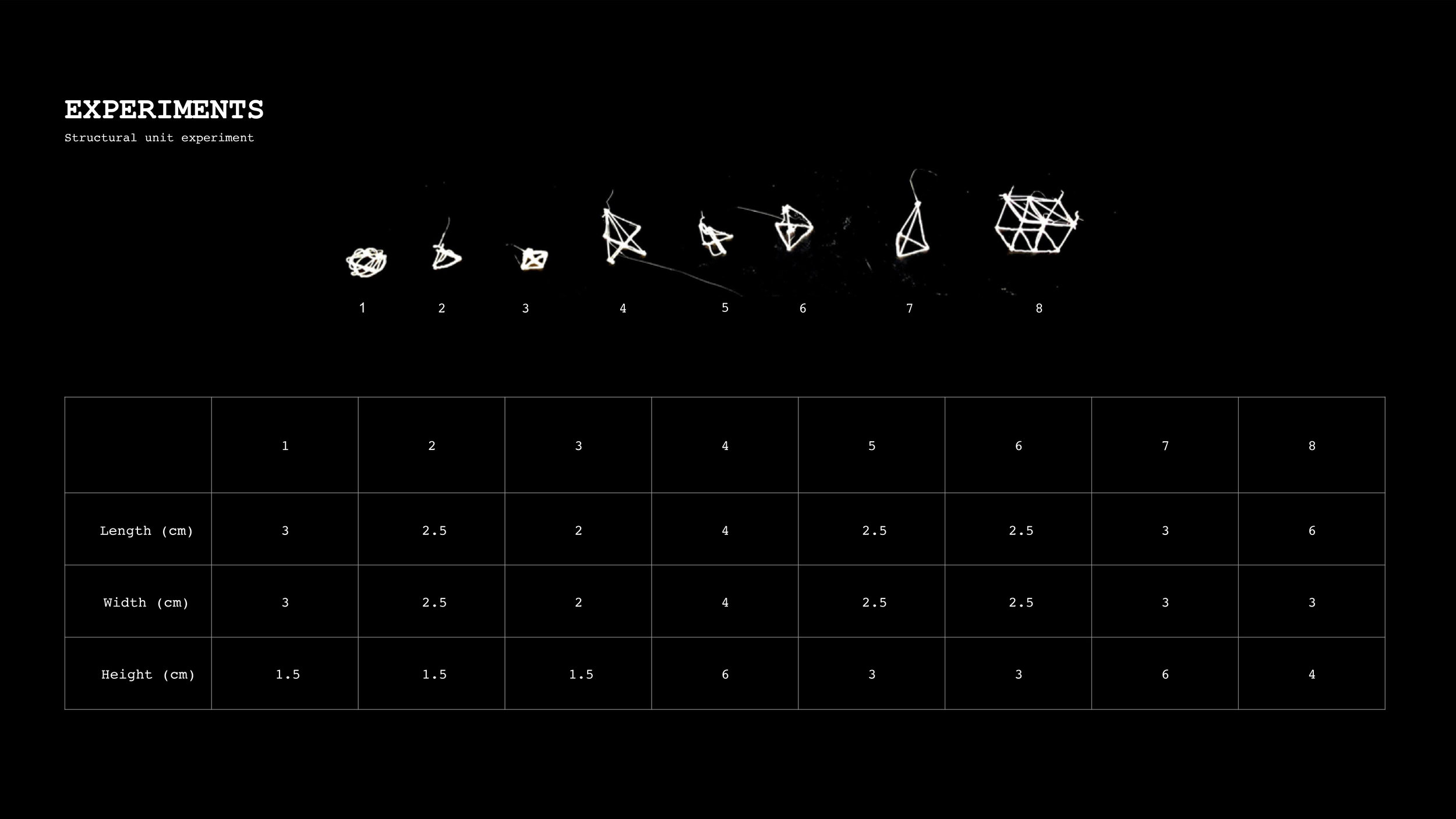
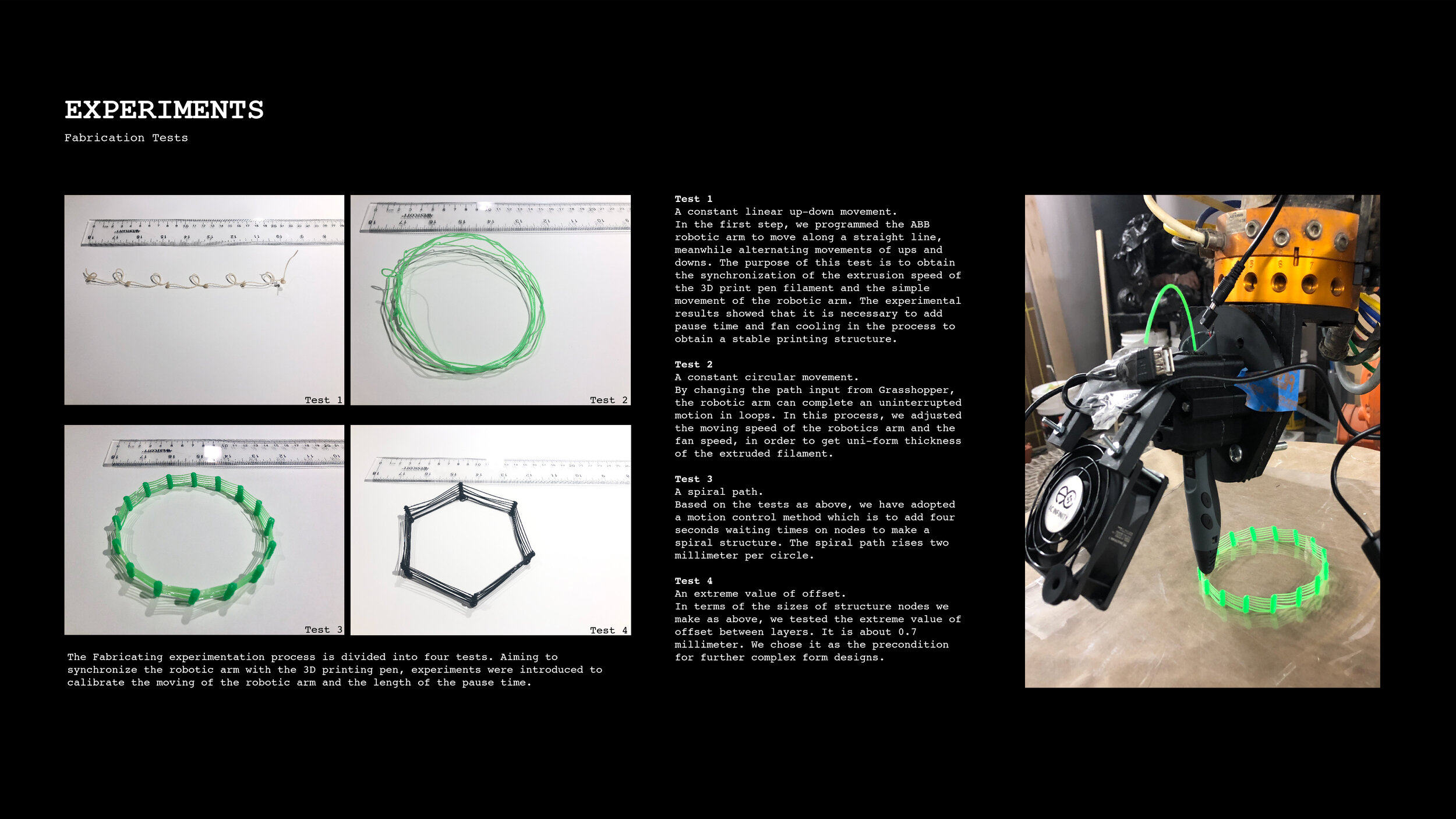
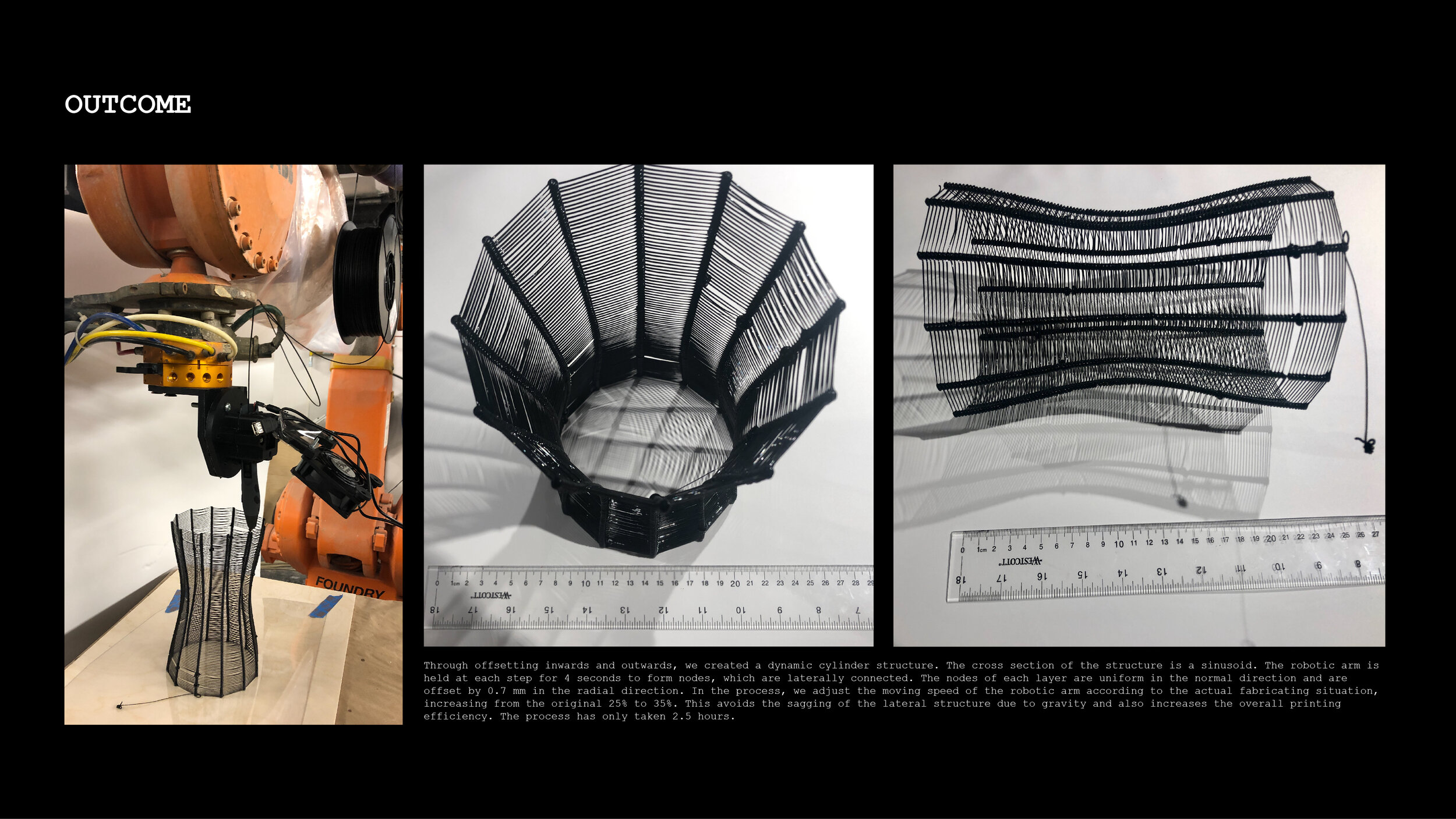
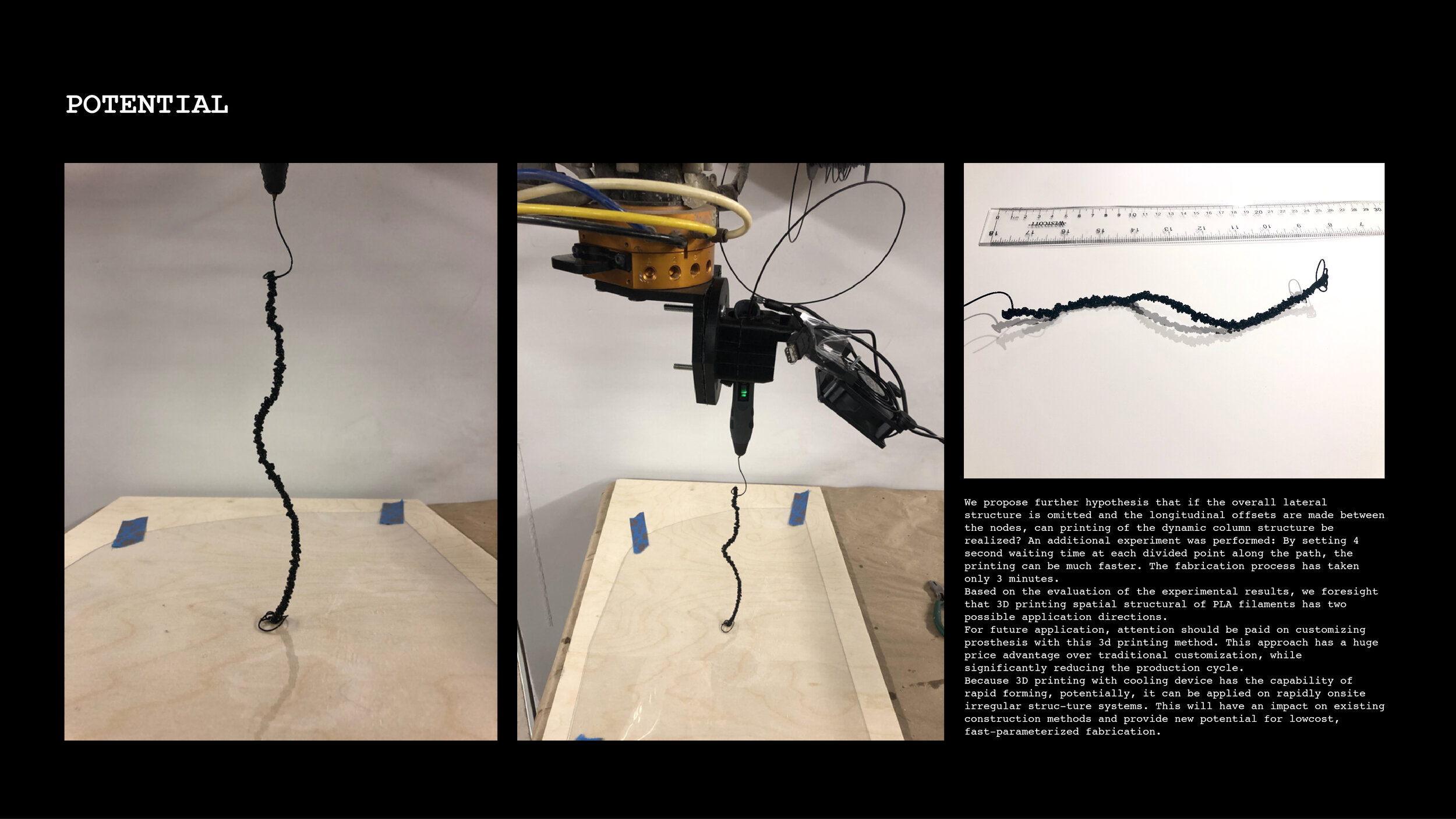
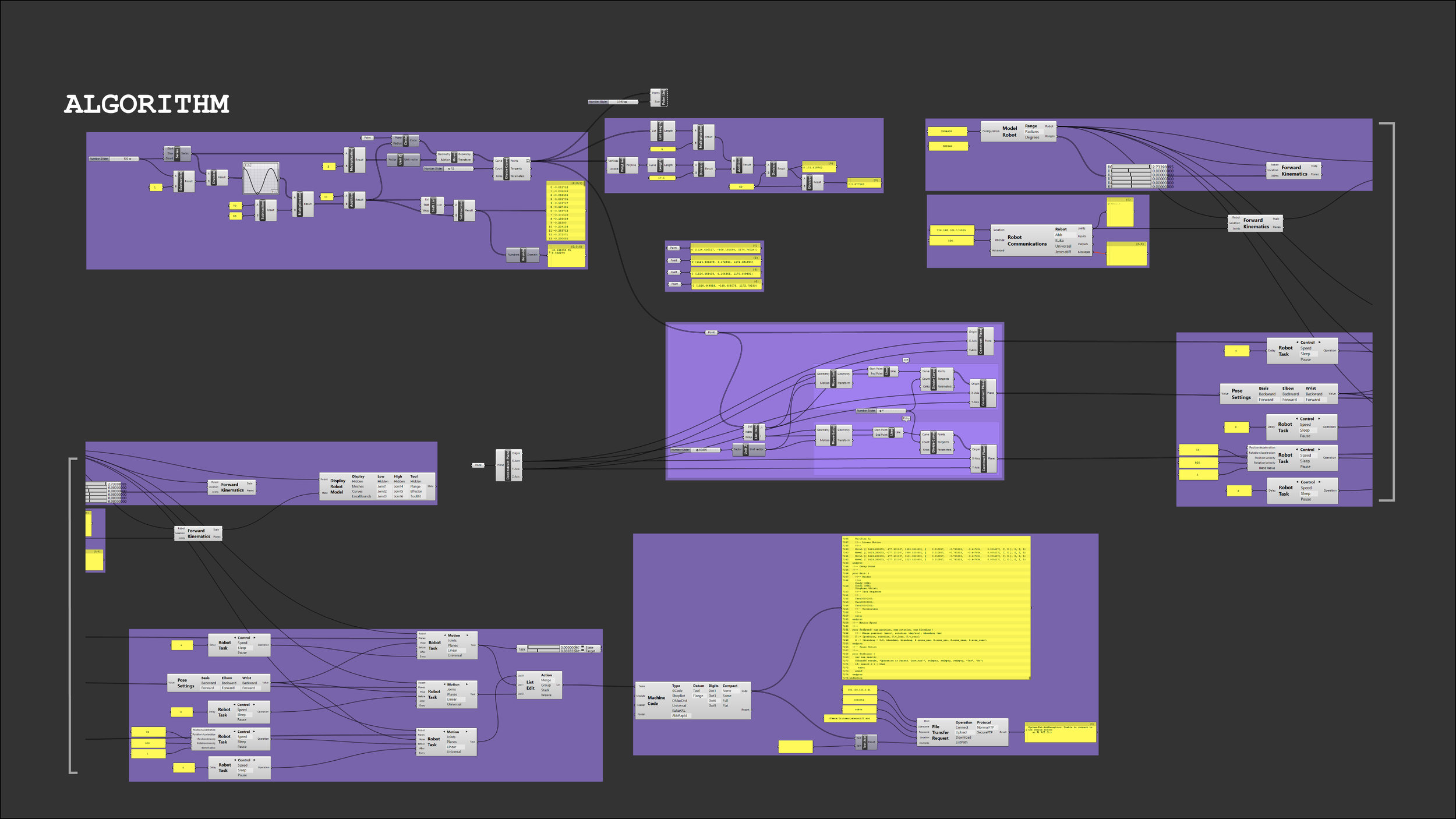
Robotic Fabrication: Printing Study on Rapid FDM Spatial Structures Beyond Size Constraints
Harvard Fabrication Lab, 2018-2019
Team member: Lubin Liu
#SpatialStructure #PathScheme #RapidFabrication #ABB #IRB-140 #Jeneratiff #Robot #FDM #DigitalFabricationStudy #SpeculativePrintingResearch #grasshopper
Tools: ABB IRB-140 robotic arm calibration & control, Grasshopper Jeneratiff Plug-in
Rethinking 3D Printing: Beyond Size Constraints
For years, 3D printing has been a game-changer in digital fabrication, transforming everything from product design to architecture. But there’s always been one major roadblock: size limitations.
Conventional FDM 3D printers operate within a fixed build volume, meaning that anything larger than the printer itself has to be assembled from smaller prefabricated parts. This not only complicates fabrication but also creates structural weak points.
What if we could break free from these limitations? That’s where robotic arms and spatial 3D printing come in. By combining the precision of a robotic arm with the continuous extrusion of a 3D printing system, we can fabricate complex spatial structures directly—without needing support materials or on-site assembly.
This isn’t just an incremental improvement—it’s a fundamental shift in how we think about fabrication, material efficiency, and architectural design.
PLA: The Material That Holds It All Together
For this research, we chose PLA (polylactic acid) filament, a biodegradable thermoplastic known for its versatility and ease of use. Its properties made it an ideal candidate for rapid fabrication in a robotic printing system:
Glass transition temperature: 60–65°C
Melting temperature: 173–178°C
Tensile modulus: 2.7 MPa to 16 MPa
Why does this matter? PLA’s rapid cooling time allows it to solidify quickly, which is crucial when printing structures without support materials. This feature helped us push robotic 3D printing beyond its traditional limits by fine-tuning the fan speed.
Experimenting with Robotic Motion & Path Planning
To make robotic 3D printing practical, we had to answer some key questions:
How do we synchronize extruder speed with robotic motion?
What’s the best way to ensure layer adhesion and structural integrity?
Can we create a self-supporting spatial structure without scaffolding?
We conducted four key experiments, each refining the system’s motion control, extrusion accuracy, and printing efficiency.
Test 1: The Basics—Linear Up-Down Movement
📌 Goal: Synchronize extrusion speed with robotic arm movement.
📌 Method: Program the robotic arm to move in a straight line, alternating between upward and downward movements.
📌 Findings:
Without pause time, the structure failed due to filament sagging.
Cooling intervals and precise timing stabilized the structure.
Test 2: Adding Complexity—Continuous Circular Motion
📌 Goal: Achieve a stable, uninterrupted looping extrusion path.
📌 Method: Program a circular movement using Grasshopper to control robotic motion.
📌 Findings:
Precise speed calibration was needed to maintain filament thickness.
Fan cooling adjustments reduced warping and inconsistencies.
Test 3: Printing in 3D Space—Spiral Path Fabrication
📌 Goal: Construct a self-supporting spiral structure.
📌 Method:
Move 2mm upward per full rotation in a spiral path.
Introduce a 4-second pause at each node to allow filament to cool before the next layer was added.
📌 Findings:
The spiral method allowed the structure to support itself without additional materials.
This proved that 3D printing with a robotic arm could work for complex freeform structures.
Test 4: Pushing Limits—Extreme Offset Printing
📌 Goal: Find the maximum feasible offset between layers before structural failure.
📌 Method:
Increase layer offset step-by-step until failure occurs.
Optimize robotic speed to prevent sagging.
📌 Findings:
The ideal offset was 0.7mm, balancing layer adhesion and geometric flexibility.
Increasing the robotic arm’s movement speed from 25% to 35% prevented lateral sagging and boosted print efficiency.
These tests proved that robotic arms offer a level of precision and adaptability that fixed-platform 3D printers simply can’t match.
Over-Extrusion: From a Defect to a Design Feature
Here’s where things get really interesting.
In traditional FDM printing, over-extrusion—where too much filament is deposited— is considered a defect. It leads to blobby prints, surface roughness, and poor resolution. But in our research, this so-called "flaw" became one of the biggest advantages.
By using robotic arms, we could control where and how over-extrusion happened, allowing the excess filament to rapidly form joints and connect structural elements seamlessly. Instead of weakening the print, this effect reinforced it, enabling:
✅ Stronger, interwoven connections between print segments.
✅ Faster volume generation, reducing print time.
✅ A new approach to freeform spatial fabrication.
What was once a problem in traditional 3D printing is now a huge advantage in robotic-driven fabrication.
Why This Matters: The Bigger Picture
Our research isn’t just about making 3D printing faster or bigger—it’s about redefining what’s possible in digital fabrication.
Key Takeaways:
🔹 No more size limits: Robotic arms allow for unrestricted build volumes.
🔹 No support structures needed: Objects can be printed in free space, saving materials.
🔹 Faster, more dynamic printing: Real-time motion control unlocks new fabrication strategies.
Future Applications: Where This Can Go Next
1. Custom Prosthetics & Medical Applications
With this level of control, custom prosthetics could be printed in a way that’s cheaper, faster, and more adaptive to each patient’s needs.
2. Large-Scale Architectural & Construction Innovations
Imagine printing entire building components on-site—no scaffolding, no prefabrication, just direct fabrication from robotic-controlled extrusion.
3. Sustainable, Low-Waste Manufacturing
By eliminating wasteful formwork and reducing material use, robotic 3D printing could revolutionize sustainable construction.
Final Thoughts: The Future of Robotic 3D Printing
This project proves that robotic arms + 3D printing can fundamentally change how we build.
By embracing new material behaviors, questioning traditional limitations, and using robotic precision to our advantage, we’re opening up a whole new era of fabrication—one where design and production are seamlessly unified.
What was once impossible in traditional 3D printing is now a powerful tool for large-scale, adaptive construction.
We’re just scratching the surface—what’s next? 🚀